Powered by the Internet, big data and other new technologies, the furniture industry has undergone rapid development of intelligent manufacturing. From traditional low-cost competition, its core competencies have shifted towards products of high added value, transforming the roles of simple furniture manufacturers to all-in furniture solution providers.
To break the development bottleneck and further deepen intelligent manufacturing in this competitive market, furniture enterprises must not only upgrade the hardware from stand-alone machinery or traditional automatic production line to more flexible PC-based smart connected manufacturing systems, but also integrate software and hardware resources and optimise configuration to build the connection interface between the store end and the factory end. When the sales end receives the order and places it with the factory, and the latter handles scheduling, order decomposition, process management, production, storage and delivery, and lastly on-site installation for the customer.
As each part of the process is closely connected and mutually coordinated, a fully closed loop from sales to production is thus formed. Based on the “device + software, online + offline” production and marketing model, and by breaking down information silos, furniture enterprises can truly conduct human-machine integration to achieve intelligent production and maximise the production capacity under limited conditions.
To facilitate the informatisation of whole-house customisation enterprises, Nanxing Machinery and FinChinaSoft joined hands to innovatively break down the complex software and hardware of Industry 4.0 into several information modules and extensible unit workstations according to working procedures and functions. Customers can flexibly choose the required units as needed, or link up the different workstations to form a complete Industry 4.0 smart production line by which boards need not reach the factory floor when processed. This module-based intelligent application integration solution has been implemented in many regions. It is extremely cost-effective, stable and efficient, and is practicable and easy to implement, thereby enhancing the manufacturing strength and competitiveness of furniture manufacturers.
SOFTWARE:
FinCADCAM→OMS→APS→MES→WMS
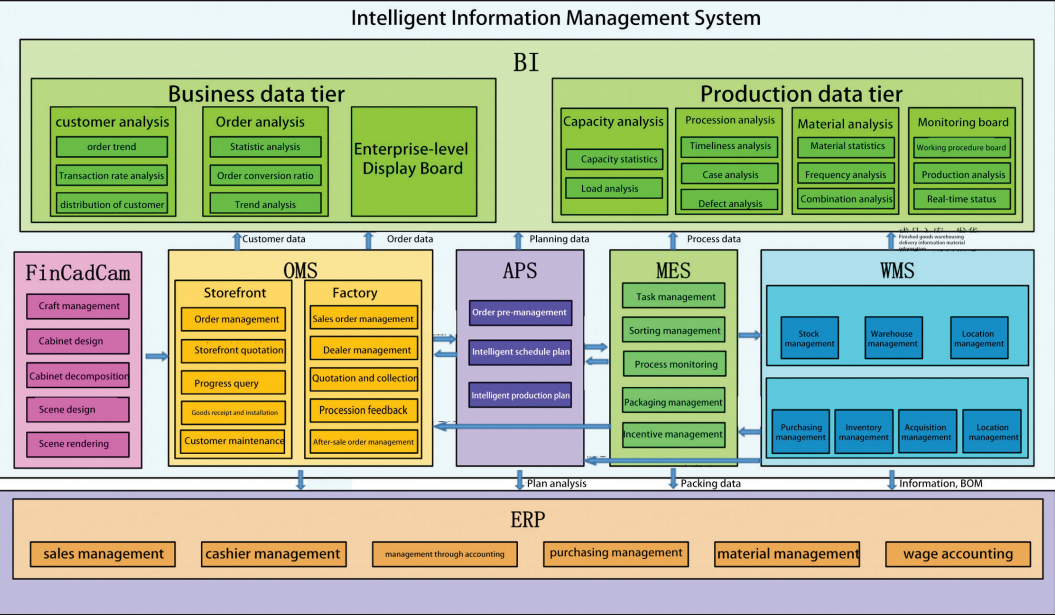
The software mainly comprises five major modules that complement each other. Sales stores use FinCADCAM to retrieve the cabinet style from the design library according to customer needs, and perform the scene rendering to retrieve the order and create theorder file. The order management system (OMS) controls the order process and data decision analysis in real time. After the order is submitted for production, the advanced planning and scheduling software (APS) performs intelligent production scheduling and sends the scheduling results to the manufacturing execution system (MES) that provides the production department with lean information solutions for the production process. These include workshop task allocation, production optimisation, production scheduling, production monitoring, order sorting and packaging. Lastly, the warehouse management system (WMS) performs storage management for finished products, and meanwhile reports the production and storage progress to the OMS at the sales end, forming a complete closed loop.
HARDWARE: INTELLIGENT
WORKSTATION = SOFTWARE
DRIVE MACHINERY + ROBOTS +
CONVEYORS
Intelligent Nesting Workstation
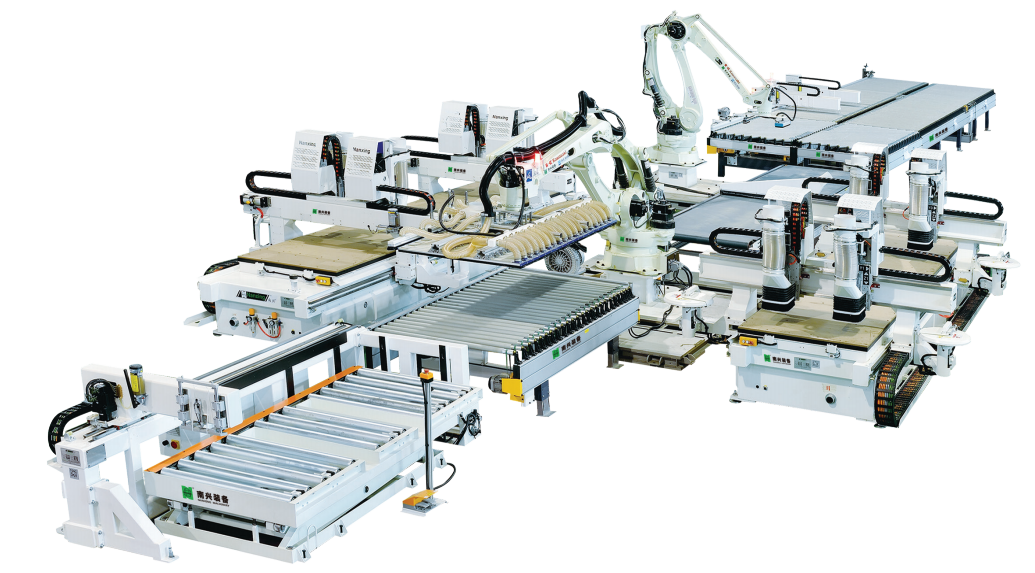
With Nanxing Machinery’s heavyduty CNC cutting device NCG2T2C4, three Kawasaki robots and conveying appliances are orderly organised through FinChinaSoft’s automatic control system (“Supervisor”) to coordinate processing and complete feeding, cutting, blanking, and labelling. The master control interfaces with the MES to exchange panel-processing data, and receives scheduling data from the APS for real-time calculations to promptly adjust and match the production capacity. With a flexible and timely production system, customers can truly use software to steer the machinery and achieve human-machine intelligent FinCADCAM to retrieve the cabinet style from the design library according to customer needs, and perform the scene rendering to retrieve the order and create the order file. The order management system (OMS) controls the order process and data decision analysis in real time. After the order is submitted for production, the advanced planning and scheduling software (APS) performs intelligent production scheduling and sends the scheduling results to the manufacturing execution system (MES) that provides the production department with lean information solutions for the production process. These include workshop task allocation, production optimisation, production scheduling, production monitoring, order sorting and packaging. Lastly, the warehouse management system (WMS) performs storage management for finished products, and meanwhile reports the production and storage progress to the OMS at the sales end, forming a complete closed loop. production, or have it connected to their own production system for independent use. Fully integrated robotic arms and machinery allow simultaneous processing of eight spindles and four stations, and can complete the fully automatic and continuous process of feeding, cutting, blanking and labelling of 400 pieces of large 4 ft by 9 ft boards per shift, reducing the waiting time. Despite having an approximate production capacity equivalent to three and a half traditional electronic saws or four engraving machines, it only occupies an area of one and a half
electronic saws and requires six fewer workers – a result of robots replacing manual labour in highintensity repetitive work. Moreover, in the aspect of processing, the milling cutter can eliminate the subsequent edge-banding and squaring process, with high processing quality and stability, and a low error rate. Due to optimisation, the board utilisation rate is greatly improved, leading to cost savings.
The intelligent cutting workstation solution allows convenient connection to other processes. It can be connected to automatic- and rail-guided vehicles, and warehousesystem of raw materials for automatic distributing, feeding and cutting. It can also be connected to the edge-banding machine and the warehouse system of finished products for cutting, edgebanding, drilling, sorting, packaging and storage, with boards not reaching the floor throughout the entire continuous machining process.
Intelligent CNC Drilling Workstation
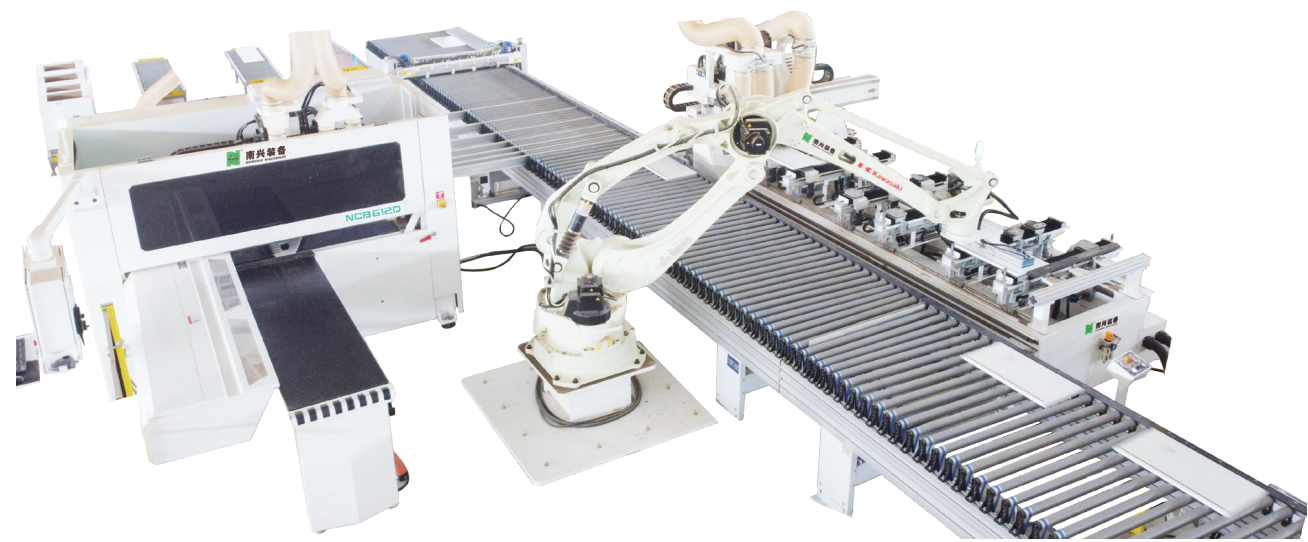
This solution is an industrial drilling unit tailored for automation transformation of large-scale wholehouse customisation manufacturers. It can be used independently or adjusted appropriately for different sites to faciliatate larger-batch production.
The workstation integrates the scanning system, Nanxing Machinery’s six-sided CNC drilling machine NCB612D and NCG3312DA PTP CNC, Kawasaki robots and conveying devices through FinChinaSoft’s “Supervisor”. NCB612D is responsible for the processing of special non-standard boards and those that require sixsided drilling, and the PTP with dual working stations and servomotor are responsible for processing relatively standard boards. The robots are responsible for the transfer and buffering of boards; the whole linedoes not require human intervention. After the master control reads the workpiece information via the scan at the start, it automatically, based on the principle of maximum production, allocates the most appropriate processing line according to the current status of equipment use and processing technique, and calls the processing programme in real time to the corresponding ones to complete the processing. If the processing area is busy, the boards are automatically transported to the buffering table for waiting. The cooperation between robots and machinery can realise intelligent, efficient and flexible drilling of workpieces. This can greatly improve equipment utilisation and production efficiency, reduce workpiece handling frequency, increase the qualification rate of products, and eliminate the inefficiency and errors caused by manual operations. The deepening of intelligent manufacturing in the furniture industry is an inevitable trend due to the rapid development of information technology and the ever-changing market demand. Nanxing Machinery’s Smart Workstation integrates mechanical equipment, robots and conveying devices with one another through “Supervisor”. One just needs to upload the APS information and MES processing data to “Supervisor” to steer the entire workstation in an orderly manner.
This module-based intelligent application integration solution is a cost-effective choice for furniture enterprises to upgrade from stand-alone production or simple automatic production lines to intelligent production, to maximise the production capacity under limited conditions.
(The article was extracted from the Panels & Furniture Asia, Nanxing)